Top Causes of PLC Control System Failure
PLC is an acronym for programmable logic controller. A PLC translates commas for machines to understand. Without PLC, actions which humans desire machines to make would be impossible for the machine to decipher. PLC translates the information a person provides a machine, such as a push of a button, and turns it into code that directs the machine to which command was given. PLCs were first developed in the late 1960s and have only become more complex and intricate. PLCs are why machines can complete specific tasks. There are some issues that still remain in PLCs, and more develop as the coding becomes more complex. When the PLC fails in a machine, the machine can no longer interpret the tasks it’s desired to complete and therefore will no longer function normally. This can be detrimental to an operation in industrial applications as it will cause large amounts of unscheduled downtime. Discover the top causes of PLC control system failure to better protect your facilities.
Module Failure of the Input/Output
This is the most common reason for PLC failures. A telltale sign of input/output PLC system failure is a sudden halt to the process or an irregular performance. This is caused because the PLC control system is waiting for a signal to usher it through a programmed sequence, but the signal is not able to reach it properly.
When this happens, an engineer must determine where the sequence originally stopped. This is typically done by an exploration of the software to trace the problem to a specific input/output module point.
Once the input/output point is identified, the engineer can follow the problem to the original cause. This typically includes PLC configuration errors, triple circuit breakers, failure of VDC supplies, issues with wirings, or even a loose terminal block. To fix this, the engineer will need to have replacement parts handy.
This entire process aims to find the disconnect between the internal situation, which is what the PLC is “thinking,” or interpreting, and the external situation, or what is actually happening.
Electrical Noise Interference
Electrical noise interference can have a large impact on the PlC control system. This typically occurs when there is foreign signal interference from electromagnetic interference or radio frequency interference.
To avoid electrical noise interference, be sure to store any large motors or similar machines far from the PLC system. The risk of this occurring also increases during lightning storms. Other causes of electrical noise interference include antennas and handheld transmitters being used nearby a PLC. This creates radio frequency interference. Any of these issues can result in extreme damage that is costly to repair. It is most ideal to avoid electrical noise interference altogether. Discussing potential options with a qualified engineer is the best method of preventing PLC control system failures due to electrical noise interference.
Power Supply Issues
Power supply issues are also common causes of PLC control system failures. PLC control systems require a steady stream of power or electricity to function as designed. When power is lost or fluctuates, the PLC can no longer function properly, and such frequent interruptions can cause complete system failure. Power supply issues can occur due to loss of power, blackouts, grid failure, old or frayed cables, loose connections, or other common electrical issues. While many of these things are virtually unavoidable, there are some ways to protect your PLC control systems, as frequent loss of power can shock the system and cause major data loss that is difficult and costly to repair.
Some of the methods of avoidance include installing a backup power source designed to activate when the main power source fails or experiences breaks. Another method is to have a qualified electrical engineer inspect and plan for the future. Also, engineers can keep batteries in their PLC systems. These batteries help to keep the system running for short amounts of time between smaller outages and issues.
Communication Issues
PLC control systems require constant communication with their surrounding and connected devices. When communication fails, the devices won’t be able to understand their required tasks as the PLC system will not be able to effectively communicate with them. This communication is usually facilitated through Ethernet cables with stable and safe connections.
To avoid these issues, PLC systems should be regularly inspected and given regular maintenance. This should be conducted by a qualified engineer who can ensure the communication network is installed properly and that all connected devices are sending out correct signals to others.
Communication issues can cause large amounts of downtime for facilities dependent on PLC control systems.
Corrupted Memory
Other external factors of the PLC control system can also cause corrupted memory. When the memory of a PLC control system becomes corrupted, the PLC’s code can become unreadable which can cause unintentional shutdown. When this issue occurs, there is no easy solution if there is no backup of the information and data on a storage device. To avoid total failure, it’s best to keep a copy of the data on a device that is stored in a safe place that is far from any potential interference, extreme temperatures, and any humidity or moisture.
There are many top causes of PLC control system failure to beware of in an operation. Contact Dreiym Engineering today for an electrical load analysis survey. In these surveys, our professional nace cp4-certified engineers conduct a survey on your facility’s electrical distribution system to determine the balance or imbalance of the system. We can then perform an electrical load assessment, starting with the creation of electrical load lists and critical load profiles. We then analyze your facility’s capacity and available provisions for future growth so that we can troubleshoot overloaded systems both for now and in the future.
Contact us today for an electrical load analysis of your facility or even your home if you’re experiencing higher billing issues, electrical usage issues, or other electrical-based problems. Our goal is to tailor your experience to your needs to not only identify and solve current issues, but also to plan for the future so issues can be avoided.
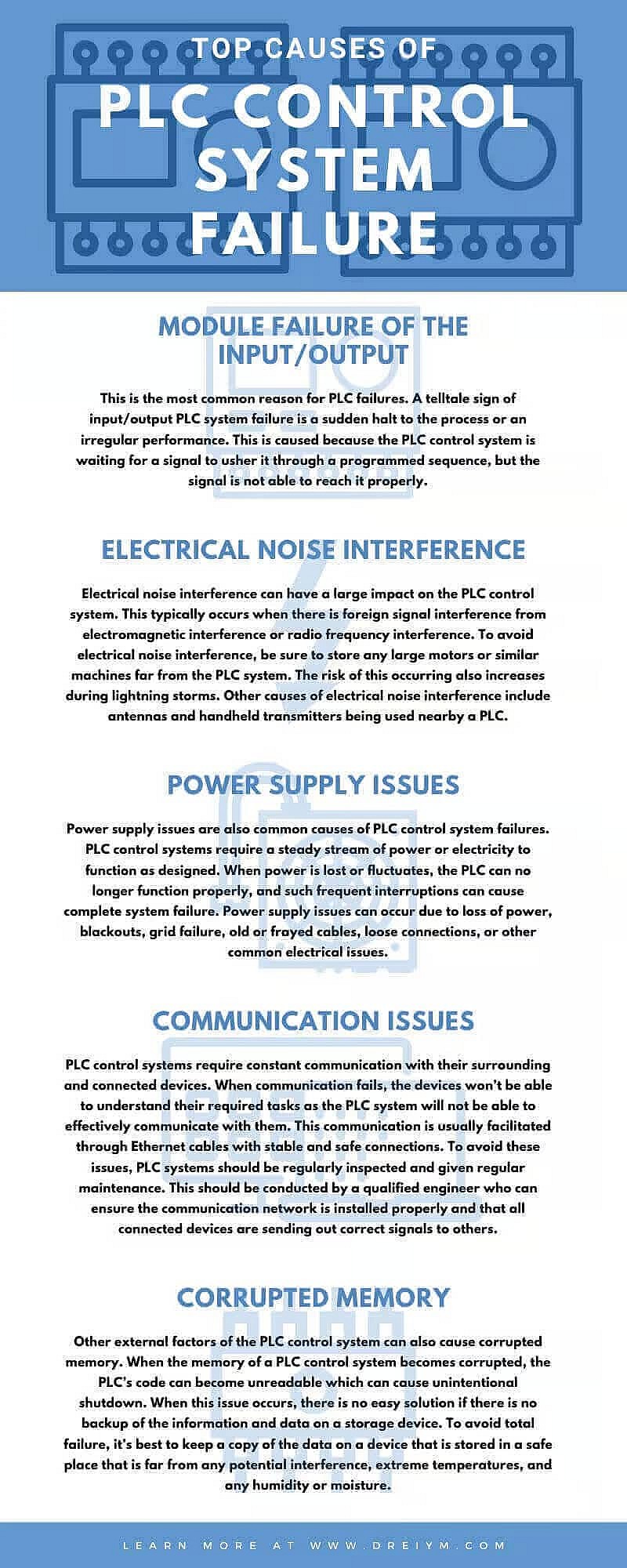